|
From user errors to equipment errors. One of the key benefits of using mobile devices and collaborative working is that the operator can receive and send all information regarding the assets in real-time at the time of inspection. Optional front and rear cameras for the Smart-Ex® and Tab-Ex® and a wireless network connection enable damage to be recorded even during inspection or maintenance. Using video telephony applications, experts or responsible employees in the control center can immediately make a remote diagnosis and initiate the necessary measures. Downtime and repair time can be drastically reduced and costly delays minimized.
Make faster and better decisions The new technologies in the Latest Mailing Database workplace, using Big Data, offers companies deeper insights into their work processes and the way they are carried out. If each user has a mobile device to collect information, the quality and accuracy of the data can be greatly improved. This is a major advantage for companies as information can be provided promptly without the need for a specialist to personally visit the facility or offshore platform. ecom's Tab-Ex® , paired with Samsung's know-how, is suitable for a wide range of tasks for a mobile user, such as inventories.
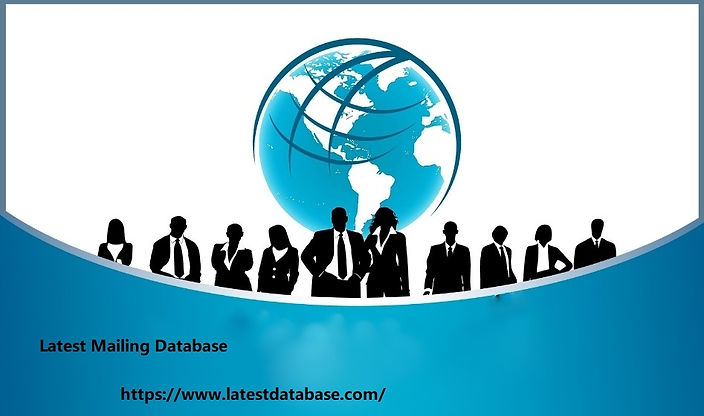
Material tracking, control rounds, inspections and maintenance. With this help, analysts can interpret the data in real time and make immediate decisions on how to proceed. Accordingly, decision-making processes can be shortened and problems or defects can be solved quickly and efficiently. Spend less time on drilling and mill rigs The less time employees spend on an offshore drilling rig or plant, the less costs the company incurs. With access to cost-effective G LTE networks in the field and offshore, the Tab-Ex® enables managers to be notified in real-time of potential plant shutdowns and anomalies.
|
|